2019 Adue SYRUP ROOM PROCESS PLANT FOR JUICE PRODUCTION
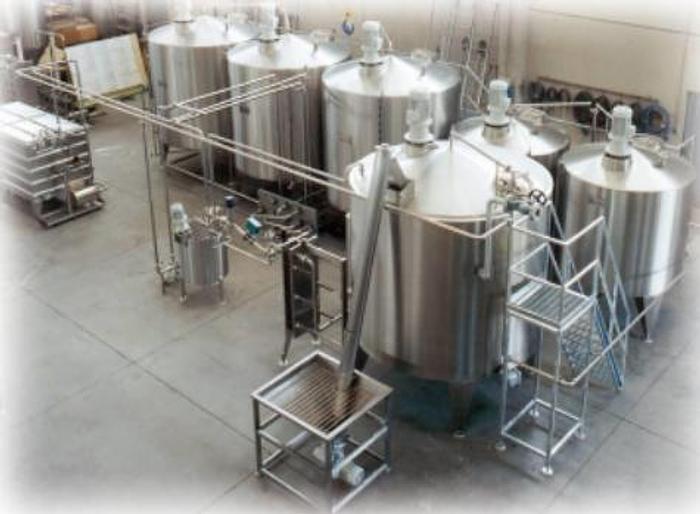
2019 Adue SYRUP ROOM PROCESS PLANT FOR JUICE PRODUCTION
Contact us for price
Nigeria
Description
SYRUP ROOM PROCESS PLANT SUITABALE FOR JUICE PRODUCTION Check PDF on website to download infos
4000 liter an hour - There are 2x Plants available (so 8000 liters an hour of juice production)
there is a water treatment plnt (12.000 liter/hour)
At the end of the line there is a Flash pasteurizer.
CIP also included.
Can produce yoghurt , ice cream, any beverage.
TO BE HOT FILLED, CAPABLE TO FEED nr. 4 FILLING LINE WITH FLOW RATE 1.500 l/h EACH FOR A TOTAL FLOW RATE OF 6.000 l/h OF FINAL BEVERAGE
Product specification
In case of ordering, detailed specification of all products are immediately required, if possible together with products samples.
The nominal outputs of the proposed plants and machinery are based on the so-called non-problematic products without major foaming such as fruit juices, fruit juices drinks, milk based products. High viscosity products or strongly foaming products may require reduction of the nominal output of the proposed plants and machinery.
Project planning
The installation of the proposed plants and machinery is done on the basis of an installation plan made by ADUE in close cooperation with the Customer, and which requires the Customer’s final approval. ADUE will supply the required documentation for the planning stage.
In case of considerable layout changes, requested after the Customer’s final approval, ADUE reserves the right to invoice the additional costs to the Customer.
Room Temperature
Parameter min. max. Unit
Temperature 15 35 °C
Humidity 30 70 %
If temperature is higher, all control boards must be equipped with Air Conditioning Units against extra cost.
Ambient Temperature
Parameter min. max. Unit
Temperature -15 50 °C
Humidity 30 90 %
Commissioning and Start up
The proposed plants and machinery will be commissioned by ADUE with 3 test productions, together with fillers, immediately after the completion of erection.
As soon as laboratory results are available, the start-up phase will be done with products and capacities specified by the Customer in a 10 – shift production, each shift consisting of 8 hours ( 1 shift / day ).
SUGGESTED WATER CHARACTERISTICS
1. Drinking water (mains water)
The drinking water should also be used as cleaning water and product flush water
The quality should meet the WHO guidelines (stated below) or European EC drinking water directive
Taste none
Smell none
Turbidity max 3 NTU
Colour max 20 mg/l Pt
Oxygen demand max 20 mg/l KNnO4
Total dissolved solids max 500 mg/l
pH (M,S) 7-8.5
Total hardness (M,S) 4-7 dH
Ammonium traces
Ammonia max 0.5 mg/l NH4
Iron max 0.1 mg/l Fo
Manganese max 0.05 mg/l Mn
Nitrate max 30 mg/l NO3
Nitrite max 0.02 mg/l NO2
Sulphate max 100 mg/l SO4
Chlorine (M,S) max 0.2 mg/l Cl2
Chloride (M,S) max 30 mg/l Cl
Aggressive corbon acid max 0 mg/l CO2
Corbon acid (M,S)
Total amount of bacteria max 100/ml
Total amount of 35°C coliform bacteria max 1/100 ml
Total amount of 44°C coliform bacteria 0/100 ml
Copper max 0.05 mg/l Cu
Zinc max 1.0 mg/l Zn
In addition:
Design pressure 300 kPa
Temperature 15°C
Capacity m3/h: AS PER QUOTATION
2. Product water is used for reconstitution of product concentrates.
Product water may not affect the essential characteristics of the product and its minimum requirement should follow the EC drinking water directive.
The reference temperature is 20 - 30°C
This means for example:
Conductivity max 400 us/cm
Chloride max 25 mg/l Cl
Sulphate max 25 mg/l SO4
Calcium max 100 mg/l Ca
Sodium max 20 mg/l No
Nitrate max 25 mg/l NO3
3 Service water to be used as cooling water, sealing water, tower water and boiler feed water.
There are different requirements for all the different types of service water.
Special attention must always be taken to hardness (CaCO3), chlorine, chloride and pH. The service water shall be without solid particles.
If unclear requirements, we recommend to use the same quality demands as for mains water.
Boiler feedwater
Hardness max 0.1 dH
Rest aluminium max 0.2 mg/l
pH 8.5-9
Silicon acid max 30 mg/l SiO2
Tower water
Design pressure 300 kPa
Capacity m3/h: AS PER QUOTATION
Temperature °C: AS PER QUOTATION
Cooling water
Design pressure 300 kPa (e)
Capacity m3/h: AS PER QUOTATION
Temperature °C: AS PER QUOTATION
Ice water
Design pressure 300 kPa
Capacity m3/h: AS PER QUOTATION
Temperature °C: AS PER QUOTATION
4 Suggested steam characteristics
Main advices:
• Steam has to be of good quality and dry.
• Steam feeding piping has to be equipped with a pressure regulator in order to keep a constant feeding pressure.
• Steam piping has to be insulated in order to avoid to hurt people.
The main features are the following:
- Pressure: min 3 bar – max 8 bar
- Quality: dry saturated steam
- Humidity : max. 5% of condensate
- Max pressure of condensate recovery: 0,5 Bar
5 Suggested electricity characteristics
The following network has to be distributed in the factory:
- Voltage : 230/ 400 V.
- Frequency : 50 Hz
- Voltage variation : max. ± 5%
- Frequency variation: max. ±-2%
- Phases : 3 + neutral
- Auxiliary : 24 V – AC/DC
Environment information
The factory is located in Lagos - Nigeria, altitude on sl less than 400 m.
Rules and Standards
Electric principle IEC (International Electrotecnic Commission)
Measurement SI (Unit International System)
Mechanic EN and UNI norms
Electric EN 60204
Tank under pressure 97/23/CE
Equipment protection degree proposed: IP 54
A DUE SRL OFFER N.0315.13.ML Rev.3 DU 27.03.20135
6 Suggested compressed air characteristics
The main characteristics are the following ones :
- Pressure : 6 - 8 bar
- Quality : dry and non-oiled air
- Water content : none
- Oil content : max. 10mg/l
- Dew point : min. 10°C less than ambient temperature
- Solid particles : max. 0.01
A DUE SRL OFFER N.0315.13.ML Rev.3 DU 27.03.2013 6
SUPPLY DESCRIPTION
SUGAR - THICKENERS - MINOR COMPONENTS & LIQUIDS INGREDIENTS PREPARATION SECTION
POS.1 N.2 MAGNETIC FLOW METER
Magnetic flow meter suitable to control the process water quantity transferred to the blending tanks, the dissolving tank and to the acid and minor ingredient
storage/dissolving tanks.
Minimum conductivity > 50 µS/cm.
POS.2 N.2 DISSOLVER DR 10
Suitable to dissolve sugar & powders, completely built in stainless steel,
equipped with:
• Stainless steel skid in Aisi 304 tickness.40/10;
• n° 04 adjustable stainless steel supporting feet;
• Hopper capacity 70 Lt.;
• Removable bag holder;
• Suction regulation manual butterfly valve Dn50 with 9 postions;
• Inlet/Outlet of the liquid with connection Dn50 F;
• Mixing chamber type “Double Vacuum”;
• Pump 4 Kw;
• Carter to cover the pump body;
• Stainless steel hopper supporting frame
• Switch control system with termic to protect the motor.
• Overall dimension: 1000x800x H=900 mm
• Weight: Kg 95;
A DUE SRL OFFER N.0315.13.ML Rev.3 DU 27.03.2013 7
Technical Features:
• Pump capacity: 15 m³/h
• Product Viscosity: ± 100 CPS ;
• Specific gravity: 1,2;
• Product Temperature: +2°/+80°C;
• Dissolution capacity: 1000 Kg/h *;
• Power supply: Multi-voltage Volt 380/660 Hz. 50;
• Injector : Made in non-toxic resin;
• Vacuum degree: -0,7 Bar
N.B.: All the parts in contact with the product are in stainless steel AISI 316 L,
the other parts are in stainless steel AISI 304.
POS. 3 N.2 STORAGE/DISSOLVING TANKS
Storage tanks, cap. 2.000 L. each on vertical axis, closed shape, equipped with agitator, suitable for Sugar, Thickeners, powders & liquids dissolution
built in AISI 316 stainless steel.
equipped with:
• n.4 adjustable stainless steel supporting feet;
• High efficiency Turbo Emulsifier agitator group on vertical axis.
• service connections;
• spray washing ball group with DN 40 connection.
POS.4 N.1 BAG FILTERS
Bag filters, flow rate 6.000 l/h for sugar syrup at 50°Bx and 25°C.
A DUE SRL OFFER N.0315.13.ML Rev.3 DU 27.03.2013 8 BLENDING SECTION
POS.5 N.4 BLENDING TANKS
type S, cap. 6.000 L each one, on vertical axis, closed shape
built in AISI 316 stainless steel.
The tanks are used to prepare the juice concentrate to feed the Blending Thanks.
Each tank is equipped with:
• conical type bottom and lid;
• electro stirrer group, on vertical axis
• n.5 adjustable stainless steel supporting feet;
• DN 400 quick-locking inspection manhole placed on the top;
• service connections;
• spray washing ball group with DN 40 connection;
• stainless steel air vent;
• level probe.
Finishing:
• welds executed in Argon inter gas atmosphere with the TIG method;
• inner welds ground and satin;
• outer welds ground and satin;
• cold rolled with 2B finishing externally;
• cold rolled with 2B finishing internally.
A DUE SRL OFFER N.0315.13.ML Rev.3 DU 27.03.2013 9
POS.6 N.2 SWING BEND PANELS
To serve the two above mentioned Blending Tanks, suitable to load the ingredients into the blending tanks, to feed the product to the Premix, for washing solutions recovery The swing bend panels includes :
• frame built in AISI 304 stainless steel .
• Automatic butterfly valves in AISI 316 stainless steel.
• connections
• connection to the tanks
POS.7 N.2 CENTRIFUGAL ELECTROPUMP
to feed the Pasteurizer, built in AISI 316 stainless steel, flow rate 3.000 l/h each.
POS.8 N.2 SELF-PRIMPING CENTRIFUGAL ELECTROPUMP
for washing solutions recovery, built in AISI 316 stainless steel, flow rate 20.000 l/ each.
POS.9 N.1 SERVICE LADDER
To serve the two Blending Tank in case of maintenance and inspections.
A DUE SRL OFFER N.0315.13.ML Rev.3 DU 27.03.2013 10
TUBULAR PRE HEATER / COOLER SECTION
POS.10 N.2 HOT FILLING TUBULAR HEATER / COOLER FOR STILL DRINK, FLOW RATE 3.000 L/H EACH FOR A TOTAL OF 6.000 L/H OF FINAL BEVERAGE..
EACH MACHINE IS CAPABLE TO FEED NR. 2 FILLERS AT THE SAME TIME
FOR A TOTAL RUNNING OF 4 FILLERS SIMULTANEOUSLY.
The Plant Is Composed By:
N.1 MULTI-PIPE HEAT EXCHANGER, TWO STAGE suitable to pasteurise with the following cycle:
• pre – heating stage from +20°C to +85°C by means of hot water circulation
• cooling stage from 85 to 45°C for the product recycling from the filler
by means of tower water
The equipment is composed by:
• stainless steel supporting frame for tubular elements;
• multi-pipe tubular exchanging elements, sanitary type with pipe for product passage in AISI 316 L, equipped with expanding compensator;
• thermometers and PT100 for working temperature control
Stainless Steel Piping
Including: pipes, fittings, valves, manual and automatic valves, deviating valves, etc
A DUE SRL OFFER N.0315.13.ML Rev.3 DU 27.03.2013 11
N.1 OVER-HEATED WATER PREPARATION AND CIRCULATION SYSTEM at 98÷100°C, servicing the pasteurisation stage, fully built in stainless steel, including: • heat exchanger water/steam without direct injection of steam in water;
• circulation centrifugal pump for water built in stainless steel;
• modulating pneumatic valve for the regular inlet of dry saturated steam at 4 Bar • pressure reducer, steam filter, manual on/off valve, pressure gauges, steam trap • hot/over-heated water connecting pipes between water preparer and tubular
elements including expanding small tank, safety valve, pressure gauge,
thermometer
N.1 CONTROL PANEL AND INSTRUMENTS including:
• PLC SIEMENS S7 to control the pasteurisation cycles equipped with software
and operational keyboard TP270 - Siemens;
• Panel in stainless steel, hinged front door, waterproof, equipped with
external air conditioner;
• Electrical part for protection and control, auxiliary circuits 24V;
• Deviation circuit for low pasteurisation temperature with alarm, silent key,
light alarm, auto/manual deviator;
• Working circuit to select production/washing/sterilisation;
The panel is placed on the en bloc base;
INSTRUMENTS
for an automatic control, recording of the pasteurisation temperature including:
• Temperature regulator range 10÷140°C, stainless steel probes, and equipped
with intervention contact in case of low temperature;
• Filter/reducer for instruments service compressed air with fittings and pipe for
reduced compressed air distribution;
• Reducer for service compressed air;
• Solenoid valves for air.
Process Description
The pasteurizer start up is with product. When the pasteurization temperature is
reached, the system gives to filler the readiness signal. In case of line stop after a settable time, the pasteurizer stops the steam feeding keeping the product in
recirculation with cooling section on, to cool down the product avoiding cooking and related damages.
When filling line is ready, the pasteurizer start feeding steam till the pasteurization temperature is reached again. When product from one batch tank is finished, the
pasteurizer stops giving indication to operator (alarm) to change the swing bend
panels. To go back to production the operator confirm operation done.
A DUE SRL OFFER N.0315.13.ML Rev.3 DU 27.03.2013 12 SANIFICATION SECTION
POS.11 N.1 “CIP UNIT 3 x 2.000 L” SANITIZING EQUIPMENT Automatic running, equipped with n°1 washing manifolds composed by:
N.1 Insulated section for the preparation of soda solution capacity 2.000 l.
cylindrical shape, built in AISI 304 stainless steel, equipped with:
• insulation on the cylindrical band;
• level probe group;
• inspection manhole;
• stainless steel adjustable supporting feet;
• safety overflow pipe outside the tank with a minimum diameter of 80 mm;
• service connections;
• finish: internally and externally 2B rolled with ground and satin welds;
N.1 Insulated section for hot water capacity 2.000 l.
cylindrical shape, built in AISI 304 stainless steel, equipped with:
• insulation on the cylindrical band;
• level probe group;
• inspection manhole placed on the lid;
• stainless steel adjustable supporting feet;
• safety overflow pipe outside the tank with a minimum diameter of 80 mm;
• service connections;
• finish: internally and externally 2B rolled with ground and satin welds;
A DUE SRL OFFER N.0315.13.ML Rev.3 DU 27.03.2013 13
N.1 Not insulated section for water recovery capacity 2.000 l.
cylindrical shape, built in AISI 304 stainless steel, equipped with:
• level probe group;
• inspection manhole placed on the lid;
• stainless steel adjustable supporting feet;
• safety overflow pipe outside the tank with a minimum diameter of 80 mm;
• service connections;
• finish: internally and externally 2B rolled with ground and satin welds;
• n°1 on-line conductivity meters to automatically recover the soda solution
with a % data readout & to control the washing solution recovery temperature;
• n°1 PT 100 to control the washing solution delivery temperature;
• n°1 thermometers to control the washing solution delivery temperature;
• n°1 pressure gauges to control the washing solution delivery pressure;
• Inlet valves of 20,000 l/h of cold water at 7/8 bar to rinse directly the utilities
to be washed cold water SUPPLIED BY THE CUSTOMER;
• n°1 centrifugal pump sanitary type for washing solution feeding
flow rate 20.000 l/h - 2,5 bar, equipped with frequency converter;
• n°1 diaphragm electro pump to dose/transfer the caustic soda concentrate;.
• n°1 diaphragm electro pump for the In-Line dosing of the disinfectant solution;
• n°1 magnetic flow meter for washing flow rate control;
• n°1 tubular heat exchangers of 500,000 Kcal/h each (maximum steam
consumption 1.000 kg/h at 4 bar), built completely in stainless steel Aisi 316,
equipped with a modulating valve to adjust the steam, a steam trap, pressure
gauges and a thermo regulator to control the temperature. The exchangers
are used to heat on recirculation (inside CIP tanks) the caustic soda solution
(or water) from room temperature to +85°C approx. during the setting the CIP
unit to optimum working conditions. They are also used to keep the
washing solution at the temperature of +85°C approx. during the washing
program.
A DUE SRL OFFER N.0315.13.ML Rev.3 DU 27.03.2013 14
N.1 Electro-Pneumatic Control Board
For the automatic management of the section, including SIEMENS S7 ‘PLC’, MP377 Siemens Touch Screen Multi Panel ‘PC’ and the electronic, electric and pneumatic instruments:
• to control the processing data;
• to control and protect the motors;
• for the signal exchange managing;
• for the integration with the CIP unit and existing syrup room;
• cubicle in AISI 304 stainless steel manufacturing;
• conditioner;
• with IP.54 protection degree;
• with auxiliary circuits 24 V.
Please Note:
The steam supply piping, the steam reduction unit up to 4 bar, the system for the
recovery and re-launching of the condensate are at Customer Charge.
A DUE SRL OFFER N.0315.13.ML Rev.3 DU 27.03.2013 15 ANCILLARY SECTION
POS.12 N.1 PIPING MATERIAL & IN-HOUSE PRE-ASSEMBLY
Piping material suitable to connect the a.m. equipment inside the syrup room,
built in AISI 316 & AISI 304 stainless steel.
The set includes pipes, fittings, valves, manual and automatic valves, gaskets,
construction material for piping supporting brackets and everything necessary for the good performance of the plant.
The processing plant scope of this supply will be in-house pre-assembled
pre-wired and pre-tested as follow:
• Ingredients preparation Section (from Pos. 2 to Pos.4).
• Final beverage preparation Section (from Pos. 4 to Pos.8).
N.B.: the pre-assembly between the Cip Unit & the above mentioned section
can be quantified & quoted upon receipt of the Lay Out the Plant.
Will not be in-house pre-assembled, pre-wired and pre-tested what follows:
• Washing delivery solution.
• Washing recovery solution.
• Process water Pipeline.
• Loading Lines of all the ingredients from their Storage/Dissolving Tanks
up to the Blending Tanks (Position 4 of this Offer).
N.B.: in any case, can be quantified & quoted upon receipt of the Lay Out the Plant.
POS.13 N.1 MATERIAL FOR THE ELECTRIC AND PNEUMATIC PLANT
Electric material for the connection of the a.m. equipment inside the syrup room.
The set includes connecting wires, stainless steel net cable tray, Rilsan pipe
electric and pneumatic accessories.
A DUE SRL OFFER N.0315.13.ML Rev.3 DU 27.03.2013 16
POS.14 N.1 ELECTRIC CONTROL BOARD
For the automatic management of the juice processing section, including SIEMENS S7 ‘PLC’, MP377 Siemens Touch Screen Multi Panel ‘PC’ and the electronic, electric and pneumatic instruments:
• to control the processing data;
• to control and protect the motors;
• for the signal exchange managing;
• for the integration with the CIP unit and existing syrup room;
• cubicle in AISI 304 stainless steel manufacturing;
• conditioner;
• with IP.54 protection degree;
• with auxiliary circuits 24 V.
Find more here - https://www.ucymachines.com/
Contact us at - sales@ucymachines.com
Specifications
Manufacturer | Adue |
Model | SYRUP ROOM PROCESS PLANT FOR JUICE PRODUCTION |
Year | 2019 |
Condition | Used |