2015 OTECO OPTIMA 12-22T-3/5,5
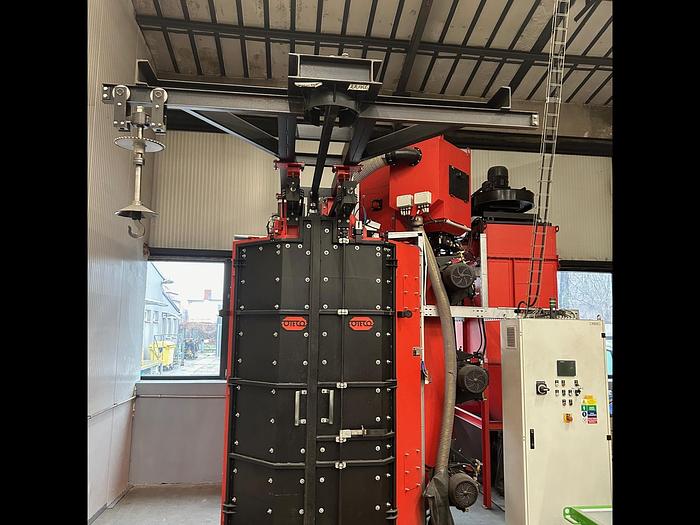
2015 OTECO OPTIMA 12-22T-3/5,5
Contact us for price
Czechia
Description
2015 OTECO OPTIMA 12-22T-3/5,5
Blasting machine for pre-treating metallic parts for powder coating.
Used in 1-shift operation with a maximum of 25-30% utilization, in top condition.
Delivery times:
Within 4 months from the signing of the purchase contract.
Guarantee:
For the scope of delivery we guarantee that it will comply with the applicable specifications and applicable technical specifications, safety and hygiene regulations on the territory of the Czech Republic.
We also guarantee in terms of the quality of the delivery for the material used, for the construction of the delivered equipment, for the function of the delivery, for the quality of the assembly work and the achievement of the quality technical parameters.
The guarantee is for a period of 24 months.
The guarantee does not apply to parts of rapid wear, whose lifetime is shorter than the guarantee period. The guarantee is further conditioned by the fact that the equipment is maintained according to the instructions for use and maintenance and is used replacement parts of the manufacturer of the equipment or parts of the appropriate quality.
Replacement parts and service:
Worn replacement parts and all electrical components will be added within 24 hours.
If the defect is reported by 12:00, the arrival of a technician is guaranteed the same working day. If the defect is reported between 12:00 and 15:00, the arrival of the technician is guaranteed on the next working day between 6:00 and 8:00.
Ownership right:
The goods remain the property of OTECO CZ, spol. s r.o. until the complete price including installation costs and VAT is paid.
This also applies to any successors of the buyer.
The labyrinth seal ensures that no abrasive or dust escapes during the nozzle. The inner sheath is protected against abrasion.
Dulezitti. innovation:
The door is equipped with an air labyrinth, which improves the efficiency of
This air labyrinth in the lower part of the door is let out into the chamber, so that abrasives cannot fall out when the door is opened!!!
Protection of the inner walls: the inner cab casing is lined on the ceiling and in the areas within easy reach of the throwing wheels with removable manganese steel plates, the other inner casing is protected against abrasion by plates and hangers made of special abrasion-resistant rubber.
Suction cascade
To maximise the efficiency of the air exchange (thus avoiding the deposition of dust on the already blasted surface), an extraction cascade is built into the rear wall of the cab.
In addition to the above advantages in maximizing the efficiency of the extraction, this supplement also serves to
cleaning of abrasives from light/1 impurities.
The hanging beam is made of profile material. It is pulled out in front of the blasting door so that the blasted parts can be conveniently loaded by means of the lifting device.
Rotary floor conveyor and rotary table:
This is a special sbemy conveyor with minimum height for transporting the blasted abrasive to the lower head of the elevator. The drive of the conveyor is electromotive. Access to the conveyor blades is from above. The conveyor is covered with a perforated manganese sheet, which allows access to the blasting cabin for the operator or maintenance.
The elevator is partially integrated into the jet cabin. The body is made of folded sheet metal and is equipped with an inspection opening. The Homi drive head is equipped with a belt tensioning mechanism. The conveyor belt is made of a special abrasion resistant material with a textile insert and is screwed with abrasion resistant plastic clips. The elevator is driven by an electric motor with gearbox.
Cleaning abrasives:
The dividing wall ensures the correct division of the abrasive so that the separation of the dust particles by means of the sucked air is optimal.
The dust collector is equipped with a suction pipe for connection to a filter with fan. Separated
impurities are discharged outside the cleaner by means of a flexible hose with a non-return valve. The cleaned abrasive falls into a silo with a separating nozzle for the bottom wheel(s).
The level of abrasive in the silo is controlled. When the maximum level of abrasive in the silo is reached, the excess abrasive falls into the blasting chamber and is again cleaned.
Abrasives:
The body of the cap is made of sheet steel. The closing mechanism is servo-controlled. (Note: this method of abrasive control can be applied for programmed blasting - change of blasting parameters (direction of nozzle tilt, change of abrasive quantity, change of abrasive speed) without the necessity of process transfer).
In front of the automatic abrasive dosing there is a built-in mechanical shut-off for the possibility of stopping the abrasive flow in case of repair or replacement of the pneumatic dosing mechanism.
Wheel throw:
The grinding wheels are in hardened (hardened) design for the nozzle.ni mixture of granulate (napf S230) and sharp-edged abrasive (napf. type GL40). The impeller assembly consists of two presses made of heat-treated steel. It is statically and dynamically balanced. Medium throwing ca.st assembly made of parts for amplitude and direction control, throwing blades (6 pcs) and armouring made of wear-resistant cast iron. Fixing of the blades is firm, but allows quick replacement. The drive is provided by an electric motor with gearbox. The power transmission is good.
Binding mechanism: assembly of:
The T-shaped binding mechanism is made of profile. The runway is fixed to the steel structure made of profile and is attached to the jet cab by means of screws.
The switching of the deflection, which enables the carriage to be moved to the left or right position, is by means of a pneumatic cylinder which is switched from the operator's position by means of a control button.
Loading trolleys: movement on the loading track is ensured by four wheels with dust-tight storage of the roller bearings. Each trolley is further equipped with a hanging hook with bronze sleeve and axial bearing, a toothed ring for rotation and simultaneous oscillation of the part in the course of the part blasting, a hook guide wheel and a protective cover.
Complete pneumatic system: assembly of:
control unit (filter - regulator - lubrication unit), solenoid valves
pneumatic cylinders and flexible hoses with quick couplings for connection of all pneumatic elements.
Electrical Engineering
The main electrical switchboard with controls is in a sheet metal box (IP 54/20), which is screwed to the side of the cab body or placed separately near the machine.
The relevant control elements, including the PLC control display, are located on the door or in a panel in the operator's position, which makes it optimally accessible in all circumstances. The price includes complete equipment for wiring, securing and controlling all parts of the device.
Even the PLC device can set up at least 80 programs for the nozzle.
Electrical equipment.
Surface treatment: 1 x overcoat + 1 x topcoat + 1 x structural varnish.
ECOLOGICAL FILTER WITH VALVE.TORUS
The OT JP filters are designed to clean the air from dry mechanical impurities. The way of cleaning of the filter cartridges (JET) enables continuous operation without the need to switch off the fan during cleaning.
The fan is placed on the "clean" side of the filter on a base which is firmly connected to the filter frame. The direction of the outlet opening is adjusted according to the requirement for optimal placement. The fan is usually connected to the filter by a pipe (made of durable plastic or steel sheet). Prufez
of the pipe is chosen so that the air velocity is within 1O and 20 mis.
CONSTRUCTION:
The filter body is made of steel profiles and sheet metal. The bottom part of the filter is in the shape of a trychtyfe and is used for collecting dust particles. Dust waste is automatically discharged through mechanical seals with anti-binding into bags made of striped plastic slats (in which it is also disposed of) stored in metal containers.
In the central part of the filter are placed filter cartridges. They are fastened by bayonet fasteners from the "quarter" side and their installation (or replacement) does not require additional force (advantageous in low halls). The middle part of the filter also contains a separation chamber, which protects the filter cartridges against possible air blows and also separates coarse dust particles. In the upper part of the filter there are solenoid valves and air pipes with nozzles for blowing. For perfect cleaning of the filter cartridges, an air pressure of approx. 5 to 6 bar is sufficient.
The filter rhythm is fully automatic and does not require any intervention of the operator.
FUNCTION DESCRIPTION:
It is a cartridge, fully automatic JET filter. Cleaning is based on the counter-current principle, i.e. from the "clean" side a short pulse of pressurized air is fed into the filter elements, which removes the trapped dust from the filter surface. This dust falls into the collecting nozzle and is discharged via a flap discharge mechanism without the need to stop the fan into the dust hopper. The time interval between the two dusting cycles and the pressure air for the blowing off of the filter bed can be infinitely regulated. In this way it is possible to select the optimum mode for cleaning the filter bed, thus achieving a long service life of the filter material, which significantly reduces operating costs.
TECHNICAL DATA:
Filter type:OT 60 JP
Design: cartridge, fully automatic
Risk: automatic with manual interval setting
Air flow: 5800 m3/hod
Number of filter cartridges: 3 ks -1
Filter housing: 20m2/
Filtration medium: polyester microfibres
Fan motor power: 5.5 kW
polyester microfibre 5,5 kW
Operating pressure: 6 bar
Total compressed air consumption: approx. 15 - 18 m3/hr at 6 bar
Total pressure difference: approx. 2400 Pa
Voltage: 400 V 50 Hz
Max. dust content in the air at the exhaust: 0,5 mg/m3
STRENGTHS:
- Continuous cleaning of filter cartridges during operation without stopping the fan.
- Optimal efficiency because the filter bed is kept clean at all times.
- The jetting process can be carried out without the need to stop for cleaning the filter.
Air piping
Used to connect the device to the automatic filter with the fan.
It is an air duct connecting all parts of the plant, which is connected directly or indirectly to the filtration.
The main part of the pipe is made of galvanized sheet metal. Some elements are made of flexible hoses (EOLO) made of abrasion-resistant plastic.
The connection between the filter and the fan is made with a flexible air element to avoid vibrations.
The fan exhaust is oriented so that the blown air is optimally distributed in the installation hall after cleaning, or so that the exhaust can be easily connected to an outlet outside the installation hall.
General provisions
The electrical wiring of the equipment assumes the following voltage values at the installation site: Supply voltage: 400 V/50 Hz
Control voltage: 240V/50Hz
Blackout: according to the applicable DIN or EN
When ordering the machine, any deviations from these values must be specified.
Special requirements for electrical and other equipment can be supplied against payment. This fact may cause an extension of the standard delivery time.
Pressure air supplied to the plant must be clean.
The equipment must be placed in a tempered room (+5...,.+. 45°C), with no contact with water.
The equipment must be placed on a sufficiently level and solid floor with adequate load capacity. It is possible (not necessary) to install the device in a cavity (concrete).
The equipment is supplied in red-black as standard. In case of request, other colour versions are also possible (please specify RAL when ordering the fitting).
The operating and maintenance manual will be delivered in Czech language.The documentation includes the EC declaration of conformity.
Part of the machine's delivery will be also a test blasting of a test sample - a cylinder of 2200 x diameter.
1200mm with the result of uniform blasting of all sides of the cylinder.
The right to technical changes not affecting the quality and function of the machine are reserved.
Find more here - https://www.ucymachines.com/
Contact us at - sales@ucymachines.com
Specifications
Manufacturer | OTECO |
Model | OPTIMA 12-22T-3/5,5 |
Year | 2015 |
Condition | Used |